Exploring Slip Rings and Split Rings in Electrical Transmission
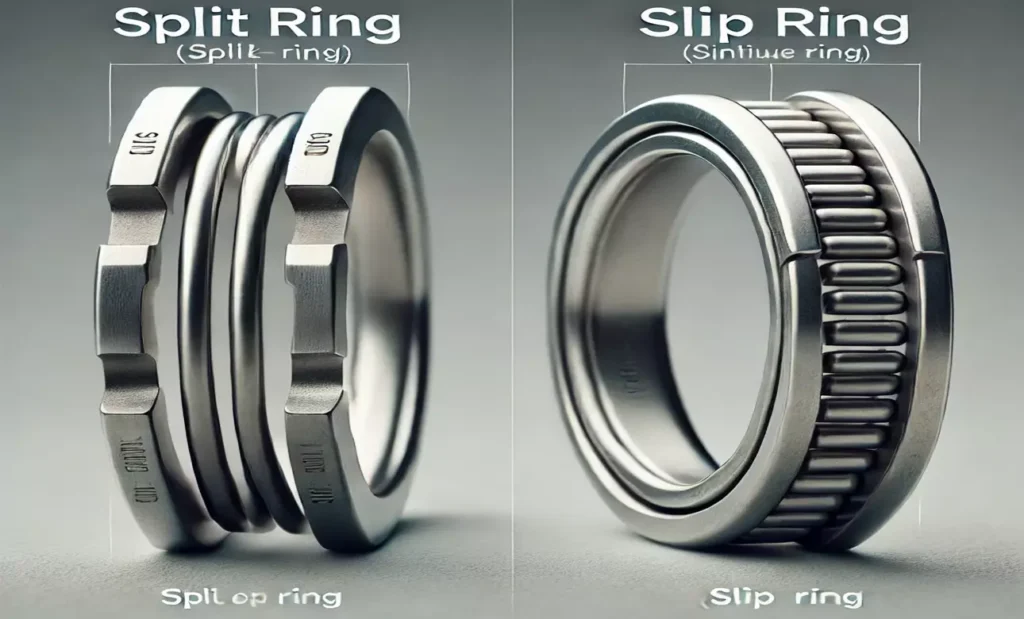
Slip and split rings are essential components in various electrical machines and systems. However, it’s important for many to understand the distinctions between these two devices. This article will explore the definitions, working principles, types, materials, applications, and critical differences between slip and split rings. We will also discuss the advantages and disadvantages of each type, maintenance considerations, and future trends in slip ring and split ring technology.
- Slip Rings
- Split Rings
- Purpose of Slip Rings
- Advantages of Slip Rings
- Limitations of Slip Rings
- Purpose of Split Rings
- Advantages of Split Rings
- Limitations of Split Rings
- Comparison of Split Rings and Slip Rings
- Practical Tips for Choosing Between Split Rings and Slip Rings
- Examples of Split Rings in Various Industries
- Examples of Slip Rings in Various Applications
- Slip Ring and Split Ring Maintenance
- Slip Ring and Split Ring Manufacturers
- Emerging Trends in Slip Ring and Split Ring Technology
- Frequently Asked Questions (FAQs)
- Conclusion
Slip Rings
Slip rings, often referred to as rotary electrical interfaces, are specialized connectors designed to transmit electrical signals and power between fixed and rotating components of a system. Unlike split rings, slip rings enable the transfer of electrical current while allowing for continuous rotation. They are composed of an inner rotor and an outer stator, with each component featuring conductive tracks that maintain electrical contact as the system rotates.
Split Rings
Split rings, also known as commutator rings or collector rings, are circular metal components consisting of two separate sections with a small gap between them. They are primarily used in electrical machinery and devices to transmit electrical current between a stationary and a rotating component. Split rings are commonly made of copper or other conductive materials and are designed to provide a continuous and reliable electrical connection.
Purpose of Slip Rings
Electrical Function
Slip rings facilitate the smooth transfer of electrical signals and power between fixed and rotating parts. Their primary purpose is maintaining continuous electrical connectivity in applications involving rotating machinery or systems.
Slip rings employ conductive rings and brushes to facilitate the transfer of electrical energy from a stationary source to a rotating component without cumbersome cables or wires. This allows unrestricted rotation while ensuring a reliable and uninterrupted flow of electricity.
Whether in wind turbines, medical imaging systems, or other high-speed rotational applications, slip rings are vital in enabling the efficient transmission of electrical energy and signals. Their electrical function is instrumental in powering and controlling various mechanisms, making them indispensable components in countless industries.
Applications in Rotating Systems
Slip rings find wide-ranging applications in rotating systems across numerous industries. They are crucial elements in wind turbines, allowing for power transmission from the fixed base to the spinning blades. In robotics, slip rings enable the seamless transmission of electrical signals and power to rotating joints, facilitating precise and controlled movements. Other applications include radar systems, crane machinery, packaging equipment, and more. With their ability to provide continuous electrical connectivity in rotating systems, slip rings play a vital role in powering and controlling various mechanisms, making them indispensable in countless industries.
Advantages of Slip Rings
Continuous Electrical Connectivity
One of the critical advantages of slip rings is their ability to provide uninterrupted electrical connectivity between stationary and rotating components. This seamless transmission of power and signals eliminates the need for cumbersome wires or cables, allowing unrestricted rotation without compromising the flow of electricity. This feature is particularly critical in applications where continuous power supply and signal transmission are essential, such as wind turbines, where slip rings ensure consistent energy transfer to rotating blades.
High Rotational Speed Capability
Slip rings are designed to handle high rotational speeds, making them suitable for demanding applications that involve rapid rotation. In industrial machinery, aerospace systems, or high-speed manufacturing processes, slip rings can reliably transmit electrical power and signals without compromising performance, even at elevated rotational speeds. This capability allows efficient operation in fast-paced environments, ensuring seamless electrical connectivity in dynamic systems.
Compact Design
Slip rings are designed to be compact, which enhances their space efficiency and simplifies their integration into a variety of applications. Their compact size ensures minimal interference with the overall system design, allowing for streamlined installations in limited spaces. This advantage is precious in industries where space optimization is crucial, such as robotics, medical devices, or automotive systems. The compact design of slip rings facilitates their seamless integration, enabling efficient electrical transmission without compromising the overall functionality and aesthetics of the system.
By harnessing slip rings’ advantages, engineers and designers can achieve reliable and efficient electrical transmission in rotating systems. Slip rings’ continuous electrical connectivity, high rotational speed capability, and compact design make them indispensable in numerous industries, enabling seamless power transfer and signal transmission in dynamic environments.
Limitations of Slip Rings
Wear and Tear
One limitation of slip rings is their susceptibility to wear and tear over time. The continuous rotation and friction between the rings and brushes can lead to gradual degradation, potentially affecting electrical conductivity. Regular maintenance and periodic brush replacement are necessary to mitigate this issue and ensure optimal performance.
Maintenance Requirements
Slip rings require regular maintenance to keep them in optimal condition. Cleaning, inspection, and lubrication are essential to remove debris, prevent corrosion, and ensure smooth operation. Failure to perform adequate maintenance can result in reduced electrical performance, increased resistance, or even system failure. It is crucial to establish a proactive maintenance schedule to address potential issues and extend the lifespan of slip rings.
Awareness of these limitations allows engineers and operators to implement proper maintenance practices, ensuring the longevity and reliability of slip rings in their respective applications. By addressing wear and tear and adhering to maintenance requirements, slip rings’ limitations can be effectively managed, ensuring continuous and efficient electrical connectivity in rotating systems.
Purpose of Split Rings
Mechanical Function
The mechanical function of split rings is crucial in various electrical systems. These rings are critical in devices that require transmitting electrical signals between stationary and rotating components. Using a split design, these rings enable seamless power and data transfer while allowing rotational movement. The split in the ring ensures that the electrical connection remains intact even as the components rotate, preventing any interruption in the current flow.
Applications in Engineering
Split rings have extensive applications in engineering. They are commonly used in electric motors, generators, and other rotating machinery. In electric motors, split rings are integral components of the commutator, which helps control the current flow direction and facilitate the conversion of electrical energy into mechanical energy. Additionally, split rings are employed in slip ring assemblies used in wind turbines, cranes, robotics, and numerous other applications where the transmission of electrical signals across rotating interfaces is essential.
These versatile components play a vital role in enabling the smooth operation of various engineering systems, ensuring efficient power delivery and seamless communication between rotating and stationary parts.
Advantages of Split Rings
Enhanced Electrical Conductivity
One of the main benefits of split rings is their excellent electrical conductivity. The continuous contact between the ring segments ensures a reliable and efficient transmission of electrical current. Using high-quality conductive materials, such as copper, further enhances the conductivity, minimizing power loss and ensuring optimal performance. This characteristic makes split rings ideal for applications that require precise and uninterrupted electrical signal transmission.
Ease of Installation
Split rings offer the advantage of easy installation. Their design allows straightforward assembly onto the rotating shaft, making it convenient to integrate into various systems. Unlike other complex electrical connectors, split rings can be easily replaced or repaired when necessary, reducing downtime and maintenance costs. This ease of installation makes split rings popular in industries where quick and efficient setup is essential.
Durability and Reliability
Split rings are known for their durability and reliability. The sturdy construction and high-quality materials used in their manufacture make them resistant to wear, corrosion, and other environmental factors. This guarantees an extended lifespan, minimizing the necessity for frequent replacements. Additionally, the simple design of split rings minimizes the risk of mechanical failure, making them a reliable choice for demanding applications that require continuous and uninterrupted operation.
Split rings’ enhanced electrical conductivity, ease of installation, and durability make them a preferred choice in various industries where reliable and efficient electrical signal transmission is crucial.
Limitations of Split Rings
Limited Rotational Speed
One notable limitation of split rings is their limited rotational speed capability. As the rotational speed increases, the centrifugal forces acting on the ring segments can lead to instability and potential damage. This restricts their usage in high-speed applications where precise and rapid rotation is required. In such cases, alternative solutions like slip rings may be more suitable, as they offer a continuous electrical connection even at high rotational speeds.
Size Constraints
Split rings are also subject to size constraints, which can limit their application in specific scenarios. The size of the split ring depends on the rotating shaft’s dimensions and the available space within the system. Finding a suitable split ring with the required dimensions can be challenging in applications where space is limited. Furthermore, the size limitations affect the current carrying capacity of the split ring, which may need to be increased for high-power applications.
Comparison of Split Rings and Slip Rings
Performance in Electrical Conductivity
In terms of electrical conductivity, slip rings have an edge over split rings. Slip rings provide continuous electrical connectivity, allowing for the seamless transfer of signals and power, even during rotational movement. This makes them highly suitable for applications that demand uninterrupted electrical transmission, such as high-speed rotating machinery or systems that require the transmission of high-frequency signals. In contrast, split rings, although capable of efficient electrical transmission, may experience brief interruptions during rotation due to the small gap between the segments.
Suitability for Different Applications
The suitability of split rings and slip rings varies depending on the application. Split rings are commonly used in applications that require a relatively lower rotational speed and where cost considerations are a priority. They find extensive use in electric motors, generators, and small-scale rotating systems. On the other hand, slip rings excel in high-speed and high-frequency applications, such as wind turbines, medical imaging systems, and robotics, where continuous rotation and uninterrupted signal transmission are essential.
Cost Considerations
Cost is an essential factor when choosing between split and slip rings. Generally, split rings are more cost-effective compared to slip rings. Their more straightforward design and ease of production contribute to lower manufacturing costs. Additionally, the maintenance and replacement of split rings tend to be less expensive than slip rings. However, slip rings may be the preferred choice in applications requiring high rotational speeds or specialized functionalities despite their higher cost.
Understanding the performance in electrical conductivity, suitability for different applications, and cost considerations of split rings and slip rings allows engineers and designers to make informed decisions based on their projects’ specific requirements. They can select the most appropriate solution for their electrical transmission needs by carefully assessing these factors.
Practical Tips for Choosing Between Split Rings and Slip Rings
Assessing Electrical Requirements
When choosing between split rings and slip rings, it is vital to assess the application’s electrical requirements. Consider the required electrical conductivity, voltage levels, and signal frequencies. Suppose you require continuous electrical connectivity, high-speed transmission, or the ability to transmit high-frequency signals. In that case, slip rings may be the more suitable option. However, split rings may suffice if the application involves lower rotational speeds and cost-effectiveness is a priority.
Evaluating Mechanical Constraints
Evaluate your system’s mechanical constraints before making a decision. Consider available space, size limitations, and rotational speed requirements. Suppose your application has limited space or requires high rotational speeds. In that case, slip rings may be the better choice due to their compact design and ability to handle higher speeds. Conversely, suppose space is not a concern and rotational speeds are relatively low. In that case, split rings may be more practical and cost-effective.
By carefully assessing your application’s electrical requirements and mechanical constraints, you can make an informed decision between split rings and slip rings, ensuring that you choose the option that best meets your specific needs and constraints.
Examples of Split Rings in Various Industries
Automotive Sector
Split rings are widely used in the automotive sector, where they play a crucial role in electric motors and generators. In electric vehicles, split rings are integral components of the motor’s commutator, enabling the conversion of electrical energy into mechanical energy. They facilitate the precise control of the current direction, ensuring efficient motor operation. Additionally, split rings are also used in generators found in traditional internal combustion engine vehicles. Their durability, reliability, and cost-effectiveness make them an ideal choice for the automotive industry.
Aerospace Industry
The aerospace industry also relies on split rings for various applications. In aircraft systems, split rings are used in electrical generators, providing the necessary electrical connectivity between the stationary and rotating components. They are crucial in maintaining a continuous and reliable flow of electrical power throughout the aircraft’s electrical system. Split rings are also used in satellite systems and are vital in power transmission and control. The aerospace industry values split rings for their ability to withstand harsh environments, deliver consistent performance, and ensure the safety and reliability of critical electrical systems.
In the automotive and aerospace industries, split rings demonstrate their versatility and reliability, making them indispensable components for efficient and precise electrical transmission in demanding applications.
Examples of Slip Rings in Various Applications
Wind Turbines
Slip rings play a vital role in wind turbines, enabling the efficient transmission of electrical signals and power between the stationary components and the rotating blades. As wind turbines harness wind power to generate electricity, slip rings allow for continuous rotation of the turbine blades while maintaining a seamless connection to the power grid. The ability of slip rings to handle high rotational speeds and transmit electrical signals without interruption makes them indispensable in the renewable energy sector.
Medical Imaging Systems
Slip rings are extensively used in medical imaging equipment such as CT scanners, MRI machines, and X-ray systems. These systems require precise and rapid rotation while maintaining a steady electrical connection. Slip rings provide a reliable solution by allowing the transmission of signals and power without interference, ensuring the accurate acquisition and processing of medical images. Their ability to handle high-frequency signals and maintain electrical integrity during complex rotations makes them critical components in medical imaging systems.
The use of slip rings in wind turbines and medical imaging systems exemplifies their versatility and importance in demanding applications that require continuous rotation and uninterrupted electrical transmission. Slip rings provide connectivity and reliability to ensure optimal performance and accurate data acquisition in these industries.
Slip Ring and Split Ring Maintenance
Regular maintenance of slip and split rings is essential to ensure optimal performance and longevity. Here are a few important maintenance practices to remember:
Cleaning and Inspection
Periodically clean the rings and segments to remove any dust, debris, or contaminants affecting electrical conductivity. Inspect them for any wear, damage, or misalignment that could disrupt the electrical connection.
Brush Replacement
The brushes are critical components in slip rings that facilitate electrical contact. Over time, brushes may wear out and require replacement. Monitor their condition and replace them when necessary to maintain consistent electrical transmission.
Lubrication
Some slip rings may require lubrication to minimize friction, ensure smooth rotation, and prevent premature wear. Adhere to the manufacturer’s recommendations for the type and frequency of lubrication to enhance performance.
Troubleshooting Common Issues
Familiarize yourself with common issues that may arise, such as poor electrical contact, overheating, or signal interference. Develop troubleshooting techniques to promptly identify and address these issues, ensuring reliable and uninterrupted operation.
By incorporating these maintenance practices into your routine, you can extend the lifespan of slip rings and split rings, enhance their performance, and mitigate potential problems that may arise over time. Regular maintenance helps ensure these vital components’ reliability and efficiency in electrical transmission systems.
Slip Ring and Split Ring Manufacturers
When selecting a slip ring or split ring manufacturer, it is crucial to consider several factors to ensure you choose a reliable and reputable supplier. Here are vital aspects to evaluate:
Major Players in the Market
Investigate and pinpoint the key participants in the slip and split ring markets. Look for manufacturers with a proven track record, extensive experience, and a strong reputation for delivering high-quality products.
Quality
Assess the manufacturer’s commitment to quality. Look for certifications, such as ISO 9001, which indicate adherence to stringent quality standards. Take into account the materials utilized, the manufacturing methods, and the testing protocols implemented by the manufacturer.
Reliability
Evaluate the manufacturer’s reliability and dependability in delivering products on time. Assess their ability to meet production deadlines, handle large-scale orders, and provide consistent product performance.
Customer Service
Assess the level of customer service provided by the manufacturer. A responsive and attentive customer support team can address your queries, provide technical assistance, and offer timely solutions to any issues arising during the purchasing process or product operation.
Customization Options
Assess the manufacturer’s ability to provide tailored solutions if your application requires specific design or customization. Look for manufacturers who offer customization options to meet your unique requirements, ensuring a perfect fit for your application.
By carefully evaluating these factors, you can select a slip ring or split ring manufacturer that delivers high-quality products and offers reliable performance, excellent customer service, and the flexibility to meet your needs. This ensures a successful partnership and the long-term satisfaction of your electrical transmission requirements.
Emerging Trends in Slip Ring and Split Ring Technology
The field of slip ring and split ring technology is constantly evolving, driven by the need for improved performance and enhanced functionality. Here are several upcoming trends to keep an eye on:
Advancements in Materials
Slash and split ring materials are being researched and developed. Innovations in conductive materials like carbon nanotubes or graphene may improve electrical conductivity, reduce friction, and increase durability. These advancements will contribute to more efficient and reliable electrical transmission.
Improved Design for Increased Efficiency
Manufacturers are continually optimizing the design of slip and split rings to achieve higher efficiency. This involves reducing energy losses, minimizing contact resistance, and improving signal integrity. Enhancing the design will result in future slip and split rings offering improved performance and higher overall system efficiency.
Integration with Smart Technologies
As industries move towards intelligent automation and the Internet of Things (IoT), slip and split rings are expected to integrate with smart technologies. This integration may involve incorporating sensors for real-time temperature, vibration, or electrical parameter monitoring. These competent slip and split rings will contribute to more efficient and reliable systems by enabling predictive maintenance and data-driven decision-making.
By closely examining these future trends, engineers and designers can stay at the forefront of slip-ring and split-ring technology. Embracing advancements in materials, improved design, and integration with intelligent technologies will lead to more efficient and advanced electrical transmission solutions for various industries.
Frequently Asked Questions (FAQs)
What are the critical differences between split rings and slip rings?
The main distinction is found in their design and operational features. Split rings are segmented rings that enable electrical transmission through physical contact between the segments. In contrast, slip rings consist of conductive rings and brushes that allow continuous electrical connectivity as they rotate.
Can split rings be used in high-speed rotational systems?
Split rings are not recommended for high-speed rotational systems due to potential instability and damage caused by centrifugal forces. In such cases, slip rings, explicitly designed for high-speed applications, are more suitable.
Are slip rings suitable for transmitting high-frequency signals?
Yes, slip rings are suitable for transmitting high-frequency signals. They are designed to maintain a stable electrical connection, allowing for uninterrupted transmission of high-frequency signals in applications such as medical imaging systems and communication equipment.
How do maintenance requirements differ between split rings and slip rings?
Maintenance requirements differ between the two. Split rings, being more straightforward in design, are generally easier to maintain and replace when necessary. Slip rings require periodic cleaning, inspection, and potential brush replacement to ensure optimal performance and longevity.
Which type of ring is more cost-effective for large-scale production?
Split rings are more cost-effective for large-scale production due to their more straightforward design and ease of manufacturing. With their more complex design and specialized functionality, slip rings often come at a higher cost.
Can slip rings be used in harsh environments?
Yes, slip rings can be used in harsh environments. However, selecting slip rings specifically designed for such conditions is crucial. Factors like temperature variations, moisture, dust, and exposure to chemicals or corrosive substances must be considered.
Do slip rings require lubrication?
Some slip rings may require lubrication to ensure smooth rotation and minimize wear. However, not all slip rings require lubrication, as some are designed with self-lubricating materials or alternative mechanisms to reduce friction and maintain optimal performance.
Can split rings be used in underwater applications?
Split rings are generally not suitable for underwater applications due to their design and the potential for water ingress between the segments, which can disrupt electrical connectivity. In such environments, alternative solutions like waterproof slip rings are more appropriate.
What safety precautions should be considered when using slip rings?
When using slip rings, proper safety precautions, including proper grounding, insulation, and adequate protection against electrical hazards, must be taken. Adhering to manufacturer guidelines and industry standards ensures safe operation and reduces the risk of accidents or electrical failures.
Are there any alternatives to split rings and slip rings?
Yes, there are alternatives to split rings and slip rings. Some other options include wireless power transmission technologies, fiber optic rotary joints, or contactless rotary connectors. These alternatives offer unique advantages and may be more suitable for specific applications where split and slip rings may not be optimal.
Conclusion
In conclusion, understanding the critical differences between slip and split rings is crucial in selecting the right type for your specific application. Slip rings provide continuous electrical connectivity, while split rings rely on segmented contact. Choosing the appropriate type ensures optimal performance and reliability in various industries, such as wind turbines and medical imaging systems.
Furthermore, the prospects for slip and split ring technology look promising. Advancements in materials, improved design for increased efficiency, and integration with intelligent technologies drive innovation in the field. These developments will lead to more efficient electrical transmission solutions, enhanced system performance, and reliability. Staying informed about the latest trends and selecting reputable manufacturers, engineers, and designers can help you make informed decisions and harness the full potential of slip and split ring technology for their applications.